Visit Green Cubes at GSE EXPO 2025, Las Vegas, NV September 16-18, 2025, Booth: 3097
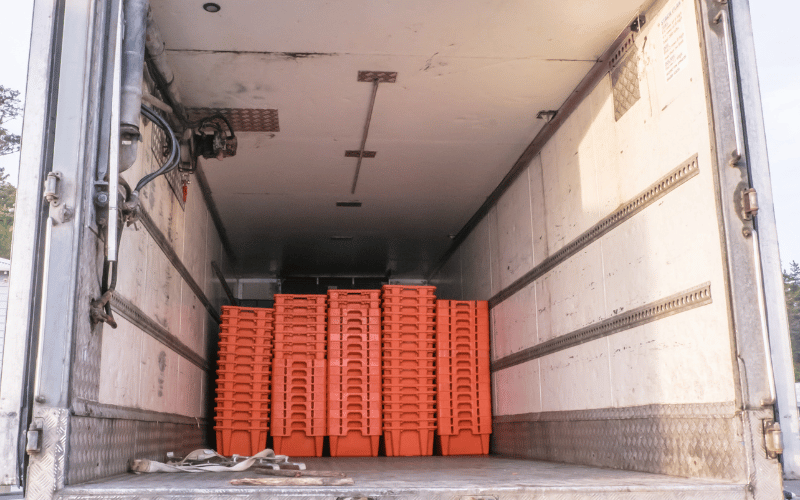
Steady power in sub-zero environments
Cold chain facilities must keep product temperatures stable from dock to trailer. Voltage sag in lead-acid batteries slows lift speed and traction as ambient temperatures drop, creating bottlenecks at blast freezers and refrigerated docks. Lithium material handling batteries hold voltage until the end of the discharge cycle, so forklifts and pallet jacks maintain rated performance even at –4 °F. Consistent travel speed keeps perishable goods moving through staging lanes before thermal exposure threatens shelf life.
Fast charging eliminates cooler-door congestion
High-traffic freezer aisles cannot spare equipment for eight-hour charging and cooldown periods. Lithium packs reach full charge in about two hours and accept opportunity charging during routine sanitation breaks. When chargers are installed beside break areas, operators top up power without extending shift length, reducing wait lines at cooler doors and keeping loading schedules on track.
Lower energy demand supports sustainability goals
Lead-acid chemistry loses roughly one-quarter of incoming electricity as heat. Lithium cells reach near-98 percent charging efficiency, an advantage amplified inside refrigeration zones where excess heat forces compressors to run harder. Switching to lithium material handling batteries can trim kilowatt-hour consumption by double-digit percentages while easing refrigeration load, helping facilities satisfy corporate carbon-reduction targets.
Minimal maintenance reduces contamination risk
Watering lead-acid batteries near food storage introduces splash hazards and airborne droplets. Sealed lithium packs never require watering, corrosion scrubbing, or acid-spill kits. Maintenance drops to quick visual inspections, freeing technicians for prevention checks on evaporator fans and door gaskets that matter more to food safety audits.
Extended life lowers total ownership cost
Lead-acid batteries average 1,500 charge cycles; lithium alternatives often exceed 3,000. Fewer replacements mean lower procurement budgets, less hazardous waste, and reduced downtime for battery swaps. Many sites redeploy capital toward insulated dock panels or high-speed doors once battery outlays decline.
Implementation checklist for refrigerated operations
- Audit current energy use, battery maintenance hours, and cooler-door dwell times.
- Verify lithium pack voltage and weight match existing Class II and Class III truck specifications.
- Position high-efficiency chargers outside freezer doors but within heated vestibules to protect electronics.
- Train operators on opportunity charging during sanitation, break, and documentation intervals.
- Monitor run-time data through the onboard battery management system to schedule proactive service.
Advance cold chain reliability today
Many refrigerated warehouses have protected product integrity, reclaimed cooler space, and lowered energy spend after adopting lithium material handling batteries. Request a customised cold chain assessment to calculate the savings your facility can realise this fiscal year.
DISCLAIMER Please note that everything posted on this site is up to date at the time of posting. Things change and products may be discontinued at any time. Please contact us for the most up to date information.