Visit Green Cubes at GSE EXPO 2025, Las Vegas, NV September 16-18, 2025, Booth: 3097
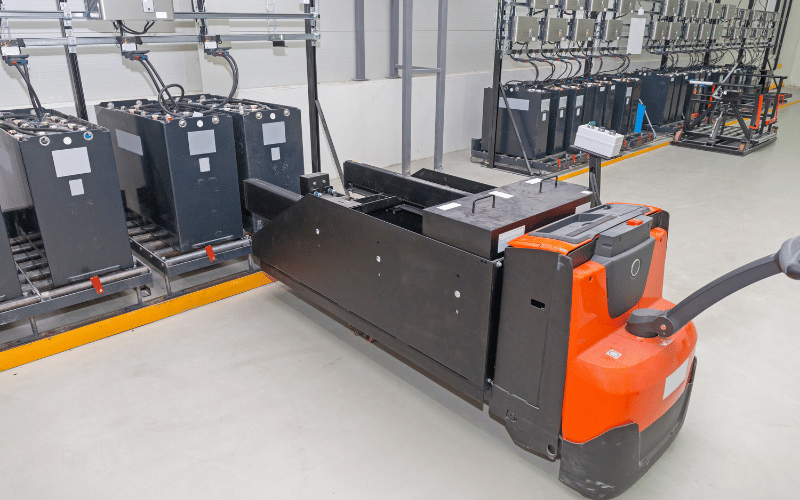
Lower ownership costs in warehousing
Warehouses monitor every dollar that flows through operations. The battery powering an electric pallet jack influences utility bills, labor schedules, and capital budgets for many years. Replacing lead-acid packs with lithium pallet jack batteries removes hidden expenses linked to watering, cooling periods, and frequent change-outs. Many facilities begin their evaluation with the Green Cubes pallet jack battery solutions page, which outlines drop-in packs for common Class III trucks.
Total cost of ownership explained
Total cost of ownership combines purchase price, electricity, planned maintenance, unplanned repairs, spare inventory, charging infrastructure, and disposal. Lead-acid packs appear budget-friendly on day one, yet often double lifetime spend once cooling intervals and hazardous-material handling are included. A properly specified industrial lithium battery keeps those categories predictable for as long as ten years, giving finance teams firmer depreciation schedules.
Energy efficiency reduces power bills
Lead-acid chemistry converts about three-quarters of incoming electricity into usable power, releasing the remainder as heat. Lithium cell designs reach more than ninety-six percent round-trip efficiency, trimming monthly kilowatt-hour charges. Operations managers who run the free TCO calculator frequently project double-digit percentage savings in annual energy spend, even before factoring peak-demand penalties.
Maintenance requirements decrease
Traditional packs demand weekly watering, terminal scrubbing, and equalization cycles. A fleet of forty lead-acid batteries can consume more than five hundred technician hours each year. Sealed lithium packs eliminate watering and spill precautions, so maintenance shifts to quick visual inspections. The onboard battery management system maintains cell balance automatically, freeing skilled labor for revenue-driving tasks.
Uptime improves productivity
A lead-acid pallet jack battery usually needs eight hours to charge and additional time to cool. Lithium chemistry reaches full charge in as little as two hours and accepts opportunity charging during breaks without shortening life. Continuous availability means fewer spare trucks, reclaimed floor space, and tighter order-cycle times.
Service life extends capital budgets
Lithium cells deliver up to three thousand five hundred cycles before capacity drops materially, more than twice the service span of lead-acid. When amortized across years of service, cost per cycle falls below fifty cents, and disposal fees drop because batteries exit service far less often. Fleet supervisors planning replacements can compare options in the material handling battery portfolio to match pack voltage and form factor.
Implementation checklist
- Record baseline energy use and maintenance labor to quantify savings.
- Verify lithium pack voltage and weight align with existing pallet jack specifications.
- Position high-efficiency chargers near break areas to encourage brief top-up sessions.
Begin your cost reduction journey
Sites that deploy lithium pallet jack batteries frequently redirect thousands of labor hours and substantial electricity spend toward growth initiatives. Request a customised quote and discover how quickly your warehouse can capture similar gains.
DISCLAIMER Please note that everything posted on this site is up to date at the time of posting. Things change and products may be discontinued at any time. Please contact us for the most up to date information.