Visit Green Cubes at GSE EXPO 2025, Las Vegas, NV September 16-18, 2025, Booth: 3097
The workhorse of your material handling equipment, batteries are quickly evolving into cleaner, better, longer-lasting models.
In the material handling world, batteries power a good portion of equipment—from most varieties of forklift trucks to AMR and AGV products. Computer carts for inventory management also depend on them. With such a central role to play, it’s important to understand what type of battery is best for your operations, how to maintain it and what the pros and cons are of the options.
Let’s start with those options. There are two common types of batteries used in material handling equipment: the standard lead acid and the newer lithium ion. The former has been around for hundreds of years and serves as the legacy battery. The latter came on the seen for material handling purposes just recently. “The technology for lithium ion was created in the 1980s, but it began with small electronic devices, like watches,” explained Maxim Khabur, Marketing Director at OneCharge. “It then moved to phones and computers, and eventually, lithium was ready for bigger formats.”
Think golf carts, forklifts and autos, where lithium now is growing in popularity. Still, while the option has been readily available for about eight years now, the material handling industry lagged in adoption rates. “Some businesses are a bit reluctant to do things different, however small the change, which is why the adoption of lithium power is not as fast as it could be,” said Khabur.
Robin Schneider, Director of Marketing at Green Cubes Technology, said that at the moment, lithium-ion batteries make up about 15% of the market. “We expect it to grow and replace most lead acid batteries over the next 10 years,” she said. “However, here are also new regulations, such as CARB, that will push general electrification and the elimination of fossil fuels. Diesel and propane are still very common, especially in outdoor equipment, but batteries and fuel cells will replace those, so it’s possible that both lead acid and li-ion batteries will grow in market share.”
As lithium options grow in availability, you’ll need to assess what best fits your particular operations. Weighing the pros and cons of each battery type will help you proceed.
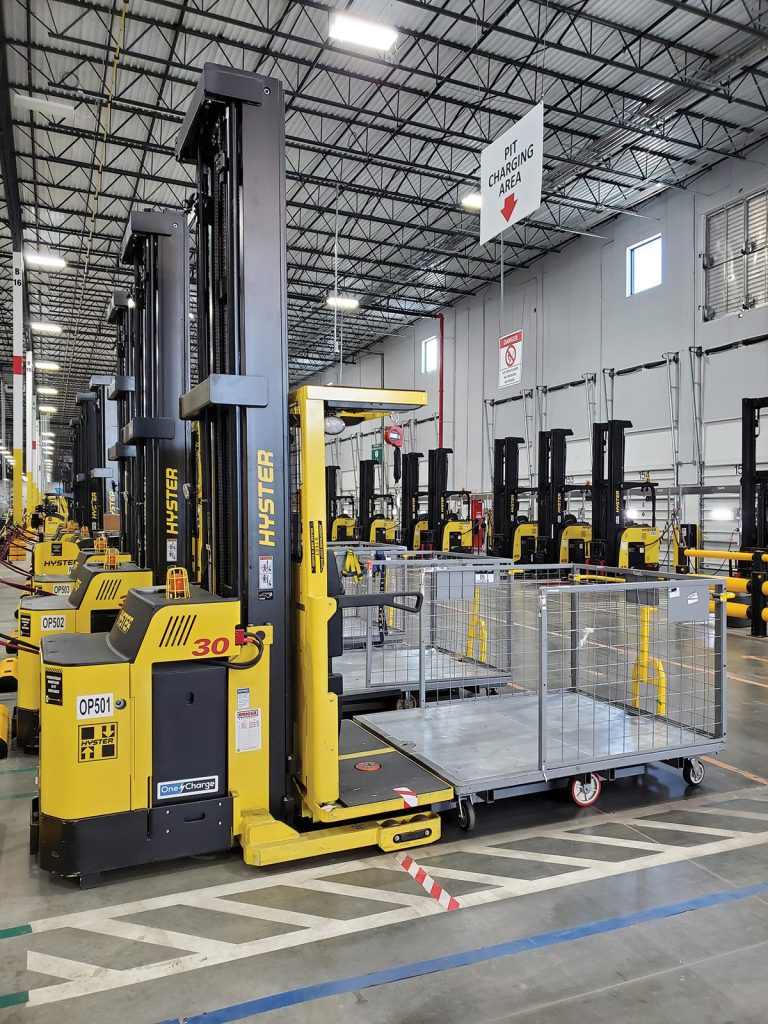
Considering Costs
The grandaddy of batteries, the lead acid battery remains a popular choice in material handling. One big reason? Price. “The upfront cost to buy lead acid is still much cheaper than lithium,” said Kevin Ledversis, Sales Director at Newcastle Systems, maker of powered carts and workstations. “But over a lifetime, lithium will come out on top.”
Still, convincing end users of that fact remains the biggest battle for battery providers. “In the warehousing space, where most companies operate on a scale much, much smaller than an Amazon, they are less likely to invest in new technology,” said Ledversis. “In these cases, they may always look for the low cost of entry versus the ROI.”
For those that do want to look at ROI as the bigger factor, the numbers heavily skew lithium over lead acid. Khabur’s numbers look like this: Over a five-year period, where an operation runs 14 lift trucks on three daily shifts, lithium batteries will cost 35% less than lead acid.
The reasons behind the lower overall lifetime cost add up through several contributing factors. Maintenance is one of them, as is the time lead acid batteries must spend out of the equipment, they power in order to charge. “Lithium-ion is maintenance free once it’s set up, has a much longer life cycle and can be fast charged,” said Schneider. “This makes it generally more cost effective over a few years’ time frame.”
Lead acid batteries also require real estate in your facility in the form of a separate charging room. “There’s a cost associated with that in the form of the ventilation required,” said Khabur. “There’s also about 30% extra electricity needed to charge a lead acid battery. The dollars add up.”
There’s also a safety factor to consider. “There are fewer injuries involved with lithium batteries,” explained Khabur, “compared to lead, which must be swapped out.”
You’ll want to consider the sloppiness of lead batteries, too. Acid spills on floors and trucks develop into corrosion, one more hazard associated with lead acid batteries.
Looking Forward
With the labor shortage in full swing—with no signs of slowing down—robots have more than proved their worth and ROI. “Robots are growing astronomically and all of them run on lithium batteries,” said Ledversis. “They are also smart enough to know where their home is and to return there for charging.”
These factors combined with many others point to a brighter future for lithium over lead acid. “Anything you power to move will be using lithium going forward,” said Ledversis. “Equipment will only become smarter and easier to use, and lithium batteries fit those applications.”
There are a few varieties of lithium-ion batteries to consider, if that’s the direction you are headed. Lithium iron phosphate (LFP) and nickel, manganese and cobalt (NMC) are examples—the former tends to feature a longer life cycle and higher power delivery, whereas NMC is more common in consumer products. MultiVoltage, a proprietary technology from Green Cubes, products are another variety and can be charged in less than an hour.
As the material handling world focuses on more sustainable options, lithium will offer the features most companies are looking for. A reduced carbon footprint, fewer fumes and acid spills and the elimination of battery charging all make lithium a greener option than its predecessor. The future will likely see everything from forklifts to robots, sweepers/scrubbers, carts, and the like powered by lithium. It may take several more years to reach that breaking point, but battery makers are confident the day is coming.
“When you add up performance, safety, sustainability and costs, lithium comes out ahead,” said Khabur. “For the material handling industry, that’s what it’s all about.” WMHS
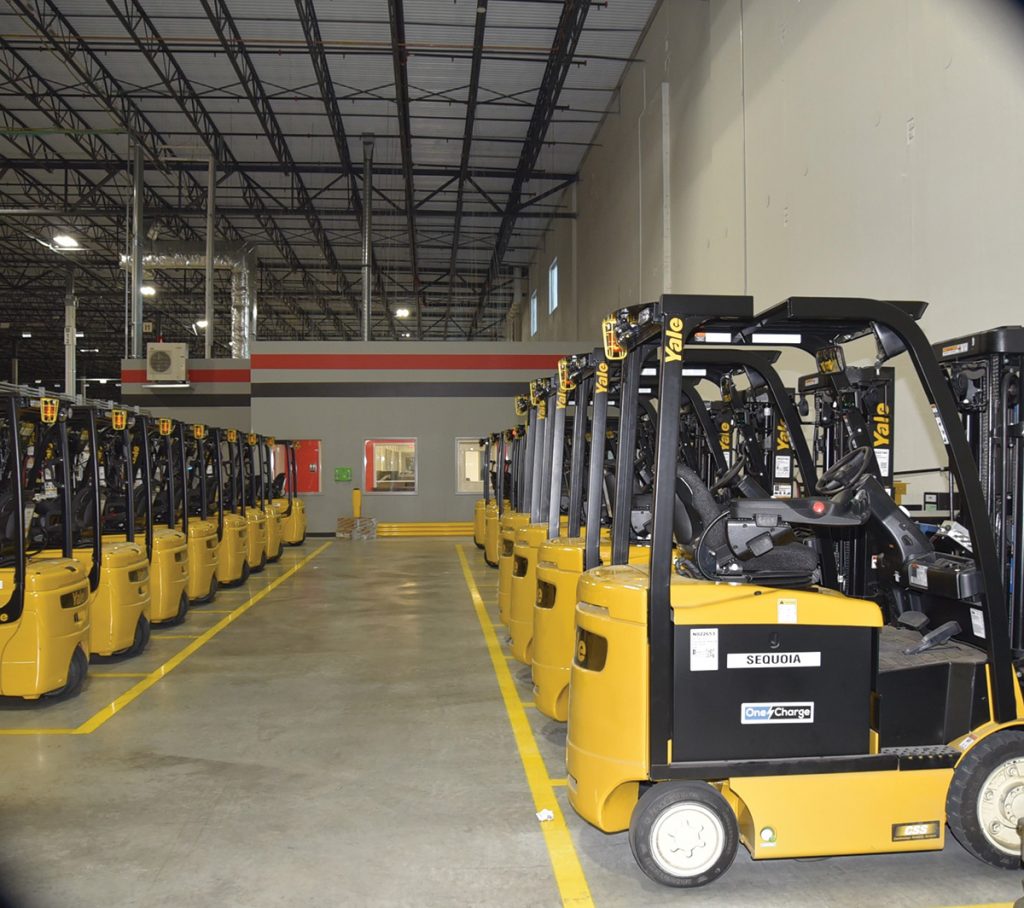
By: Christian Dow, Contributor
Read the original article at Workplace Material Handling & Safety.
DISCLAIMER Please note that everything posted on this site is up to date at the time of posting. Things change and products may be discontinued at any time. Please contact us for the most up to date information.