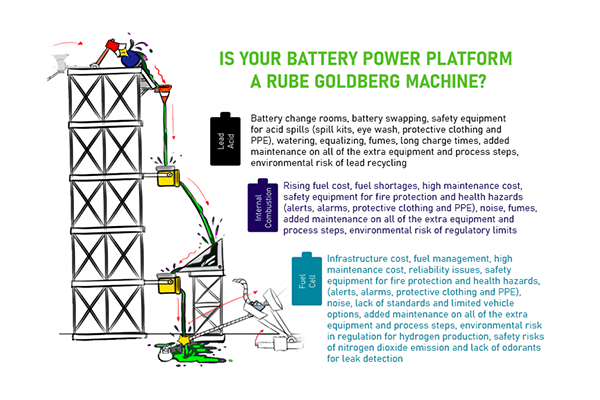
For both our employees and community, I want to address the health, safety, and environmental problems with Lead Acid. The single-biggest environmental issue with Lead-acid batteries involves the Lead component of the battery. Lead is a heavy metal with dangerous health impacts. Ingestion of Lead is especially dangerous for young children because their brains are still developing and Lead is a neurotoxin. Historically, sources included Leaded gasoline, Lead-based paints, and tin/Lead solder used in electronics manufacturing, pipes, and building construction, but those have largely been eliminated over the years. According to the World Health Organization (WHO), today around 85% of the world’s Lead consumption is for the production of Lead Acid batteries.
To mitigate the risk of the toxic impact, the often-cited claim is that Lead-acid batteries are 99% recyclable. However, Lead exposure that takes place during the mining and processing of the Lead, as well as during the recycling steps is the very source of environmental contamination and human exposure. There are many places where the process is poorly controlled often carried out without the necessary processes and technologies to control Lead emissions.
The California Department of Toxic Substances Control (DTSC) has written extensively on the case of Exide Technologies, a Lead-acid battery manufacturing company. Exide had to close down a large battery recycling plant in California after it failed to meet emission controls and waste management standards. California regulators believe as many as 10,000 homes could be contaminated with Lead from the plant. The cleanup will take many years and cost hundreds of millions of dollars. As a business, Exide has gone through multiple bankruptcies due the environmental impact cost of Lead. Battery recycling plants in other states have also been cited for contaminating the environment with Lead.
The WHO has reported cases where contamination from Lead-acid battery recycling resulted in a number of negative health effects — including the harm to children. Thus, while the 99% recycling claim sounds impressive, it understates the problem of Lead contamination via the recycling process. The situation would be much worse if these batteries are not recycled, as a single Lead acid battery in a landfill has the potential to contaminate a large area and cause harm to thousands of people. The health, safety, and environmental risk of Lead recycling far outweighs the benefit, particularly now that Lithium offers a clean, safe, and cost-effective alternative. From a productivity point of view, distribution centers that use electric lift trucks go through so many complicated steps to make Lead Acid work, including:
- Battery change rooms
- Extra batteries needed to support high volume operations
- Safety equipment for acid spills (spill kits, eye wash, protective clothing and PPE)
- Blood testing of employees for Lead poisoning
- Watering
- Equalizing
- Fumes
- Long charge times, waiting, and down time
- Maintenance on the added equipment and process steps
- Inaccurate fuel gauges and unknown cycle life due to deep discharge effects
With our customers, this means providing clean reliable energy storage and motive power for industrial applications. The complexity of the process to make Lead Acid batteries work would make any Rube Goldberg Machine maker proud. This “machine” concept is named after the American cartoonist Rube Goldberg, whose cartoons 100 years ago often depicted devices that performed simple tasks in indirect convoluted ways. It’s well past time for Lead Acid to have a place in the real world of industrial energy storage and motive power applications. It’s time to get the Lead out of batteries and the contamination of our environment from the Lead recycling process. It’s time to move to Lithium SafeFlex and the opportunity to realize the benefits of clean, reliable, innovation.
Keith Washington – CEO