There has been a lot of talk lately about new lithium-ion factories coming online and even more planned. What are they building though? Manufacturers are looking at how the size of the cell used in these EV’s can influence performance and Tesla’s new Giga factory in Austin Texas just began rolling vehicles off the line powered by a new Lithium-ion cell. Now Panasonic has delivered their first larger cells to Tesla in June, and they are big!
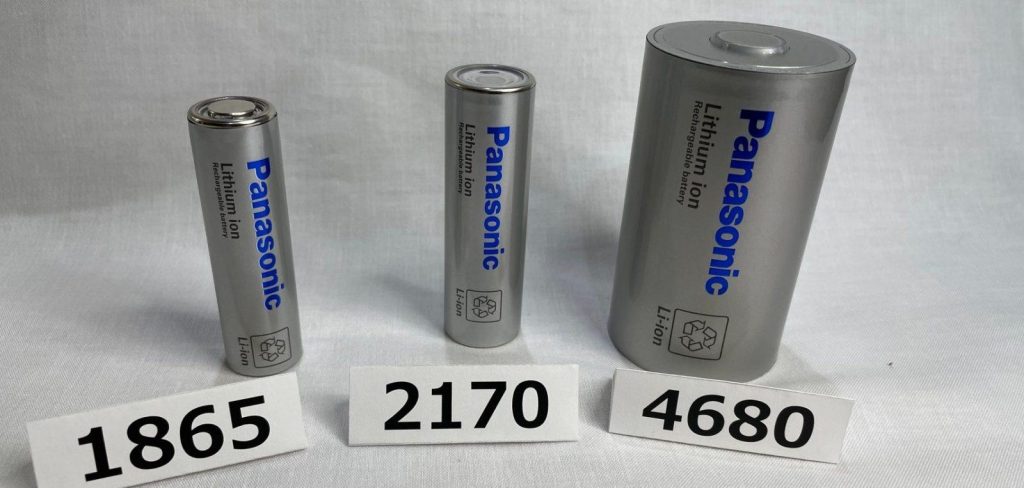
Figure 1: Lithium-Ion cells from Panasonic in three assorted sizes.
The first commercialized Lithium-ion (Li-ion) cells were cylindrical in shape. This allowed for high-speed automated manufacturing processes to be used. The original size was 18 milimeters in diameter and 65 millimeters in length (the 18650 form factor, the trailing 0 means it is a cylindrical cell, as square cells would have a third number here). These dimensions allowed for the first commercial laptops to use Li-ion cells and remain fairly slim. As the industry matured, and manufacturing ramped up to build more cells for applications, we learned that making bigger and longer cells can lower the cost of cell manufacturing. The standardization of the 18650 cell form factor spread across many industries and cemented it as the de facto shape and size.
To achieve the cost savings, a new size emerged, the 21700 cell. This introduced a 50% increase in capacity with only a 15% increase in diameter. Tesla led the charge and soon all of the major Li-ion cell manufacturers began to produce their own 21700 cells. Not only did this help increase the ratio of active material to packaging, delivering higher capacity, it also provided more active surface area for the lithium-ion exchange to occur. These cells deliver higher current and better performance.
In 2020, at Tesla’s Battery Day event, Elon Musk and Sr. VP of Powertrain and Energy Engineering Drew Baglino, introduced the world to the “perfect size”. The Tesla duo introduced the 4680 form factor (Dropping the last zero, per Elon, “Nobody could explain to me why there was an extra zero. So I… said, okay, well, we’re deleting the zero”). This new cell is 8x the size of an 18650 and provides more capacity due to the increased ratio of packaging to active materials. According to Tesla, this is the perfect size based on their analysis of the chemistry, construction methods, application needs, and manufacturing capabilities.
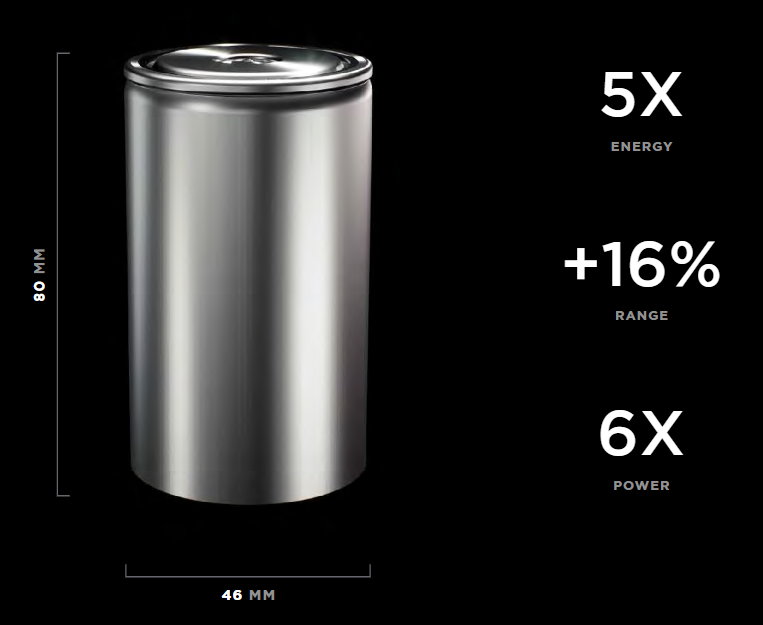
Figure 2: Tesla’s new 4680 cell
However, here are a few problems with this new form factor that will need to be solved to commercialize and ramp production. The innovation Tesla presented to solve many of these challenges is a new “Tabless” cell concept. This is multi-tab design that resembles a shingled spiral of tabs that have been laser cut on the side of the anode and cathode. What does this design do for performance? This significantly reduces the electrical path thus reducing the internal resistance of each cell, allowing the larger cells to discharge and charge quickly without generating hot spots internally and reducing the heat generation in each cell in general. This improves upon the incumbent design most cell manufacturers use today that require 1-3 tabs be placed on the anode and cathode strips, which can be over a meter long, to transport current form the active materials to the contacts on the cell.
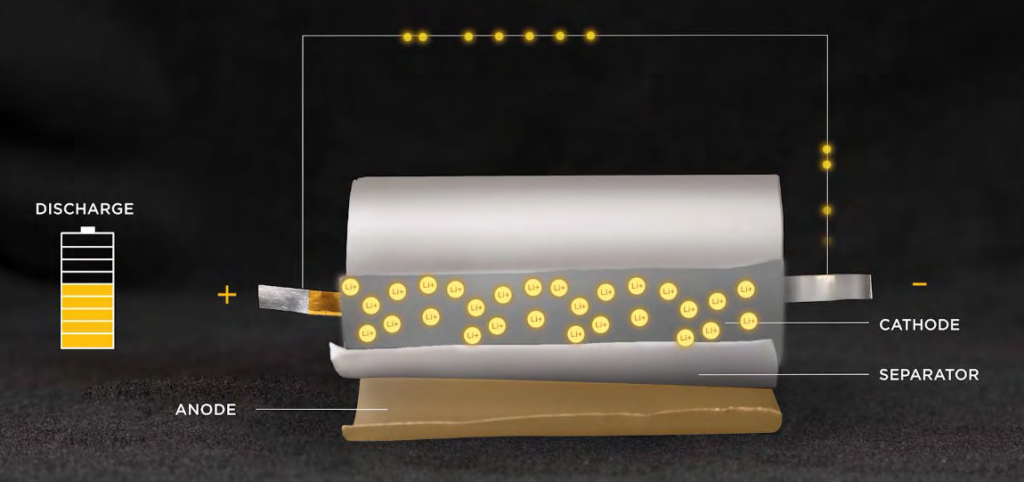
Figure 3: The Jellyroll and tabs in a typical lithium-ion cell
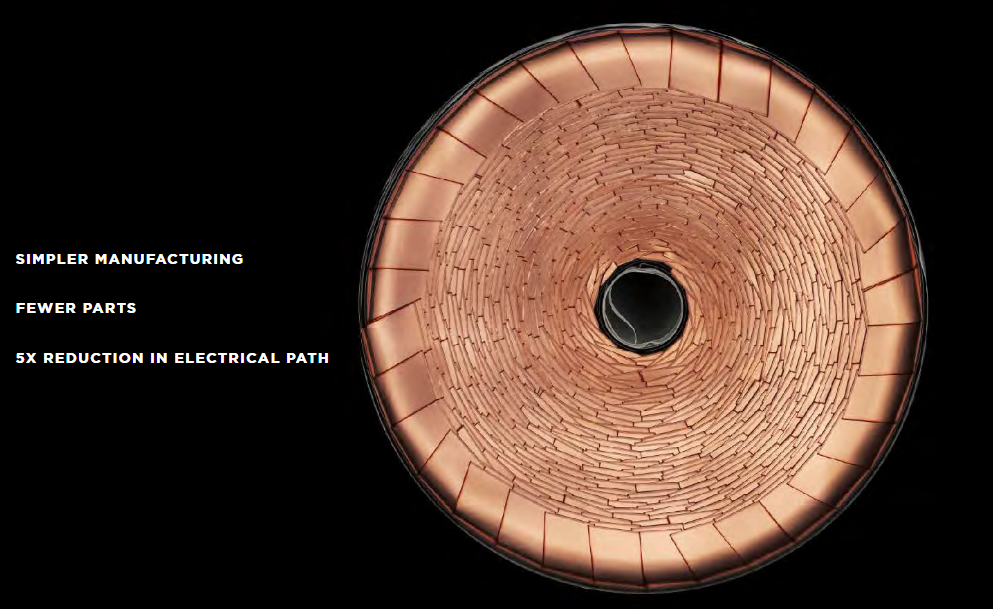
Figure 4: Looking into end of the jelly roll, this is the “Tabless” design
The clever Engineers over at Bosch Research have long thought there could be advantages to this type of mechanical approach and went the extra mile to simulate it! Their research is fascinating; they found this approach to achieve a 10% improvement in 18650s and even more in larger cells enabling higher charge rates, and most significantly reduces heat generation, resulting in lower cell temperatures.
How big is too big? The limiting factor indeed seems to be the heat rejection in the cell. Now that the heat generation has been reduced through the “Tabless” design, all cell manufacturers must determine what the optimal cell diameter is. The Bosch Engineers thought of this as well and have conducted studies to create models of the heat rejection from inside the cells. This is where Tesla, Samsung, LG, Panasonic and other manufacturers are limited in size. The rate at which heat is rejected radially is much lower than longitudinally due to the materials used in the anode and cathode of the cells. The “Tabless” design will increase the heat rejection rate longitudinally even more, but where is the sweet spot in terms of diameter? Bosch has developed the software to simulate these complex interactions, but it seems that Tesla has decided that sweet spot is at 46mm diameter, and 80mm of length.
The first 4680 cells are rolling off the line at Tesla Austin, and other manufacturers are being urged to speed up their development of this form factor as well. It seems for now that 4680 is the right size and the length of time between standard industry size evolutions is decreasing. Green Cubes is a cell agnostic Lithium Battery Manufacturer. We can use any size cell and benefit from the economies of scale, performance improvements, and diversification of supply to best serve our customers. Green Cubes is leading the charge to modern electrification using the best cell for the job.
If you would like to learn more about Bosch Research simulations, read Jake Christensen’s blog post.
If you want to know more about Tesla’s new batteries, read this article.