Visit Green Cubes at GSE EXPO 2025, Las Vegas, NV September 16-18, 2025, Booth: 3097
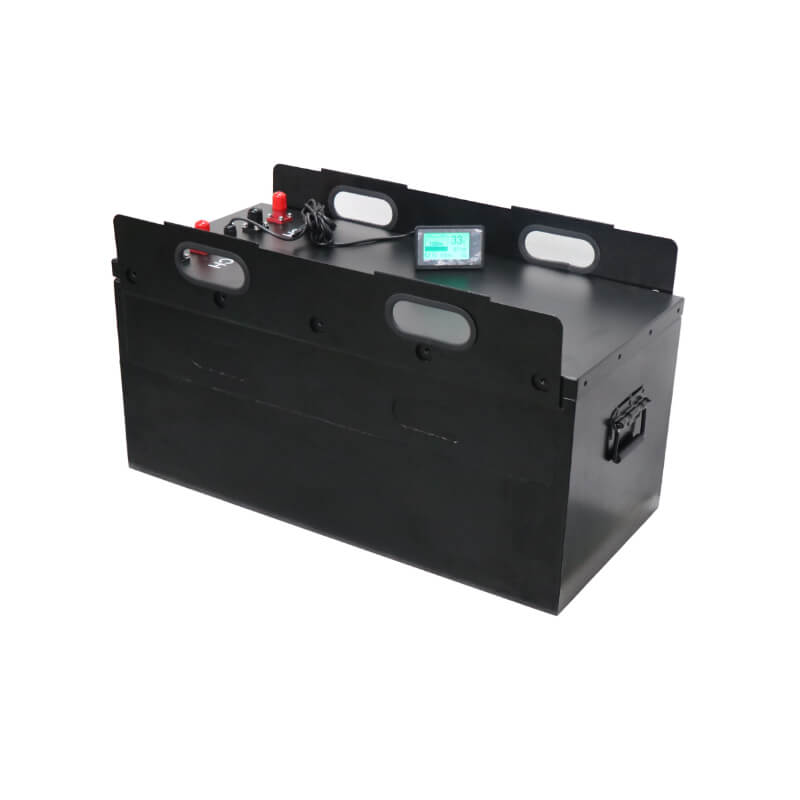
Material handling batteries power essential equipment like forklifts and pallet jacks in industries worldwide. Safety is paramount in these operations, and recent advancements in battery technology have significantly improved safety standards.
Material handling or industrial or traction batteries are rechargeable power sources for electric material-handling equipment.
Safety is crucial in material handling operations due to heavy machinery and bustling activity. Recent innovations in battery technology, including lithium-ion batteries and advanced safety features like battery management systems (BMS), have revolutionized safety standards.
In this blog post, we’ll explore these advanced safety features of modern material handling batteries and their impact on workplace safety.
Advanced Safety Features in Material Handling Batteries
Thermal Management Systems
Temperature Monitoring: Advanced thermal sensors continuously monitor battery temperature in real-time, preventing overheating and reducing the risk of thermal runaway.
Active Cooling Systems: Implementation of cooling mechanisms such as fans or liquid cooling systems to dissipate heat and maintain safe operating temperatures, ensuring battery safety during prolonged use.
Overcharge and Over-discharge Protection
Smart Charging Technology: Utilization of advanced chargers with built-in intelligence to regulate charging currents and prevent overcharging, preserving battery health and safety.
Battery Management Systems (BMS): Sophisticated BMS algorithms monitor battery state-of-charge and automatically cut off power when the battery approaches critical levels, preventing over-discharging and extending battery lifespan.
Cell-level Monitoring
Individual Cell Monitoring: Cell-level monitoring systems track the health and performance of each battery cell, detecting abnormalities such as voltage imbalances or capacity degradation in real-time.
Fault Detection: Early detection of cell faults or malfunctions enables proactive maintenance interventions, reducing the risk of safety incidents and ensuring consistent battery performance.
Impact-resistant Designs
Rugged Construction: Material handling batteries, especially those used in forklifts, feature robust casing and internal structures designed to withstand impacts and vibrations common in industrial settings, thereby ensuring durability and safety.
Shock-absorbing Components: The incorporation of shock-absorbing materials and design features in batteries for forklifts minimizes the risk of damage from collisions or drops, preserving the integrity of both the battery and the forklift equipment.
By integrating these advanced safety features, modern material handling batteries provide reliable power while mitigating safety risks, ensuring a safer working environment for personnel and equipment.
Safety Standards and Regulations for Material Handling Batteries
Existing Safety Standards for Material Handling Batteries
The material handling industry operates within a framework of established safety standards and regulations aimed at safeguarding personnel and assets. One such standard is the ANSI/ITSDF B56.11.6, which provides guidelines for the safe use of industrial trucks, including recommendations for battery handling and maintenance. Compliance with these standards is essential for ensuring workplace safety and avoiding potential liabilities.
Compliance Requirements for Different Industries
Various industries, including warehousing, logistics, and manufacturing, are subject to specific compliance requirements concerning material handling operations. These requirements may vary based on factors such as the type of equipment used, the nature of operations, and regulatory mandates. Adhering to these regulations is not only a legal obligation but also a fundamental aspect of maintaining a safe working environment.
Importance of Adhering to Regulations
Compliance with safety standards and regulations is critical for mitigating risks associated with material handling batteries. Failure to comply can result in accidents, injuries, and costly damages to equipment and facilities. By adhering to established guidelines, organizations demonstrate their commitment to workplace safety and uphold their responsibilities towards employees and stakeholders.
The Future of Material Handling Battery Safety: Trends and Developments
In the material handling industry, safety is paramount, and advancements in battery technology play a crucial role. Here, we delve into the emerging trends:
Emerging Technologies
Cutting-edge thermal management systems and sophisticated battery management systems (BMS) are revolutionizing safety. These systems regulate temperature, detect issues in real time, and ensure optimal charging protocols, mitigating safety risks.
Predictions for the Future
Predictive maintenance algorithms and advancements in battery materials promise longer lifespans and reduced downtime. These developments not only enhance efficiency but also bolster safety by minimizing the risk of battery-related incidents.
Integration with Industry 4.0 and IoT
Integration with Industry 4.0 and IoT enables real-time monitoring and predictive analysis of battery health. By leveraging data insights, businesses can implement proactive maintenance strategies, optimizing safety and efficiency.
Putting Safety First: Modern Battery Solutions
As the backbone of material handling operations, the safety of batteries is non-negotiable. Through innovative design and advanced technologies, modern material-handling batteries prioritize safety at every turn. From preventing thermal runaway to withstanding impacts, these batteries exemplify the commitment to creating a secure working environment. With ongoing advancements, the future promises even greater strides in safety, ensuring that material handling operations continue to thrive with peace of mind.
DISCLAIMER Please note that everything posted on this site is up to date at the time of posting. Things change and products may be discontinued at any time. Please contact us for the most up to date information.