Lithium SAFEFlex Battery Charger winner of the 2022 class of NED Innovation Award. The Lithium SafeFlex Battery Charger is designed to operate with material handling and other industrial equipment Lithium-ion batteries. Each model supports up to three simultaneous charging ports and performs voltage auto-detect, so it can charge a variety of industrial trucks simultaneously. This charger has CANBus communications with the battery and a touchscreen display.
Blog
Green Cubes Technology’s Lithium SAFEFlex Battery Charger Wins NED Innovation Award
Product chosen from thousands of award nominees that redefine their markets for a smarter, more efficient manufacturing world.
Green Cubes, the leader in producing Lithium-ion (Li-ion) power systems that facilitate the transition from lead-acid batteries and Internal Combustion Engine (ICE) power to green Li-ion battery power, today announced its Lithium SAFEFlex Battery Charger was named a New Equipment Digest Magazine Innovation Award winner for the Electrical and Electronics Category.
The Lithium SAFEFlex Chargers, announced earlier this year, were developed to complement Green Cubes’ market leading Lithium SAFEFlex Batteries. Green Cubes is the only manufacturer to offer enterprises both Lithium-ion batteries and affiliated Li-ion chargers to the Material Handling industry, thus simplifying the electrification of Material Handling equipment. These chargers are offered in 15 Kilowatt (kW) and 30 kW models. Each model supports up to three simultaneous charging ports and performs voltage auto-detect for each of the charging ports. Efficient Li-ion charging of multiple trucks lowers utility costs for enterprise customers.
“For the past 85 years, New Equipment Digest has been bringing the world information about not just the best equipment from the best suppliers, but also the newest, freshest designed equipment makers have developed to produce ever stronger, smarter, and more efficient tools for the manufacturers who depend on them,” said Laura Davis, editor for the magazine. “This process is really what is at the heart of NED and exactly what we look for as we curate material for every new issue—its innovation in its purest, most material form.”
The NED innovation Awards program, now in its sixth year, is an annual contest that evaluates thousands of innovative new products published over the course of 12 months to recognize those few that best represent the potential in the market. Products that fundamentally change their markets, crush limitations of their product class, and redefine design possibilities are nominated for the awards.
About Green Cubes Technology
Green Cubes Technology develops and manufactures safe and reliable electrification solutions that enable its OEM and enterprise customers to transition from Lead Acid and Internal Combustion Engine (ICE) power to Lithium-ion battery power. Green Cubes utilizes proven hardware and software platforms to build the most reliable Lithium power solutions in its industries. With over 300 employees across six countries, Green Cubes has been producing innovative, high-performance, and high-quality power solutions since 1986.
Green Cubes Announces IEC Certification of 48 Volt Lithium-Ion Battery Backup Units for Telecom and Data Center Market
Lithium Guardian Batteries provide safe, reliable, low cost energy storage for mission critical system operators
Green Cubes, the leader in producing Lithium-ion (Li-ion) power systems that facilitate the transition from lead-acid batteries and Internal Combustion Engine (ICE) power to green Li-ion battery power, today announced International Safety Certification IEC 62368 certification of the Lithium Guardian Battery Backup Units. The Lithium Guardian family of backup batteries are designed for rack mount installations in the Telecom and Data Center industries.
The Telecom and Data Center facilities operate 24 hours a day, 7 days a week, supporting mission critical functions. Traditionally, large lead-acid batteries are used to provide backup power. Li-ion batteries allow operators to store more energy in smaller spaces to power equipment longer when the grid power goes is unavailable. Lithium Guardian batteries serve this market by providing safe, clean, and reliable backup power in a small, lightweight, and cost-effective package.
The Guardian product family provides complete power system solutions to telecom and other 48V system operators with products providing rectification, power management, and energy storage. The Lithium Guardian Battery Unit (GBU) is a 48V, 105 Ah, 5kWh Lithium Iron Phosphate (LFP) battery offering reliable energy storage in a small lightweight form factor. With a design life of over 10 years, and well over 3500 cycles the LFP GBU provides operators with a long lasting energy storage solution.
“Safety and reliability are paramount to our requirements when designing Li-ion batteries. We verify our designs are safe and reliable for their application by real world testing and certification to globally recognized IEC standard,” said Mike Davis, Chief Revenue Officer at Green Cubes. “Lithium Guardian Batteries were designed to operate with a wide range of equipment; from radios, routers, to HVAC, our batteries must work. Achieving IEC 62368 assures customers that these batteries will provide power to their equipment safely and reliably.”
IEC 62368 is an internationally recognized standard to verify safety and reliability of electronic devices in telecom applications. The Green Cubes GBU has been evaluated by engineers and tested in the lab to ensure that when integrated in operator systems the battery will remain safe and not adversely affect other equipment. Previously, the Lithium Guardian 3U battery has been tested and certified to UN 38.3 for international shipping. The Guardian Lithium Batteries are currently under evaluation with multiple industrial and telecommunication operators. Commercial shipments are scheduled for December 2022.
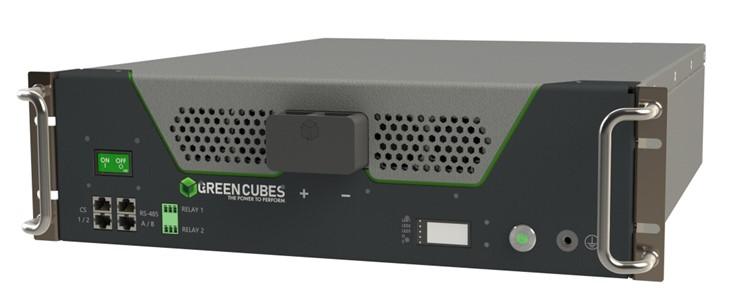
To learn more about the Guardian Product family and the Lithium Guardian batteries visit: https://greencubes.com/products/batteries/
About Green Cubes Technology
Green Cubes Technology develops and manufactures safe and reliable electrification solutions that enable its OEM and enterprise customers to transition from Lead Acid and Internal Combustion Engine (ICE) power to Lithium-ion battery power. Green Cubes utilizes proven hardware and software platforms to build the most reliable Lithium power solutions in its industries. With over 300 employees across six countries, Green Cubes has been producing innovative, high-performance, and high-quality power solutions since 1986.
Warehousing Logistics International: Best Practices for Using Lithium-Ion in Cold Storage Facilities
Temperature-controlled supply chain is more important than ever during with today’s volatile supply chain. On-line ordering of pre-prepared food, beverage clubs, and medicine distribution are all increasing the need for cold-chain technology. Lithium-ion batteries charge faster, and opportunistically, and have longer run-time than traditional lead acid batteries, optimizing equipment utilization Batteries don’t need to be swapped, watered, or equalized at room temperature, so maintenance is simplified. Cold-temperature cycle life is vastly improved for a lower total cost of ownership. This is a brief overview of how to implement and take advantage of this new technology.
Best Magazine: Green Cubes Technology launches Swappable Industrial Battery
Lithium battery maker Green Cubes Technology of the US announced a Swappable Mobile Power (SMP) portfolio of swappable lithium batteries.
Workplace: Green Cubes Technology Announces Swappable Industrial Battery for Mobile Workstation and Motive Product Manufacturers
Green Cubes Technology (Green Cubes), the leader in producing Lithium-ion power systems that facilitate the transition from lead-acid batteries and Internal Combustion Engine (ICE) power to green Lithium-ion battery power, announced its Swappable Mobile Power (SMP) portfolio.
MHI: Lead-Acid or Lithium-Ion: Batteries in Material Handling
Batteries are often taken for granted, but they can have an incredible effect on your distribution center or warehouse. Join us as we talk with Robin Schneider from Green Cubes about the batteries in your operation.
The New Warehouse: Green Cubes Technologies
On this special episode of The New Warehouse Podcast, we get an education on Lithium 101 with Robin Schneider, Director of Marketing at Green Cubes Technologies. Green Cubes is a power technology provider for customer OEM batteries, batteries for stationary equipment like data centers, and the motive business that makes batteries and chargers for material handling equipment and ground support equipment you would find at airports. If you are curious about lithium-ion batteries and what they can do for warehouses and material handling operations, you will want to tune in.
Green Cubes Technology Announces Swappable Industrial Battery for Mobile Workstation and Motive Product Manufacturers
Swappable Mobile Power (SMP) portfolio enables the electrification of mobile and motive products with swappable battery technology
Green Cubes Technology (Green Cubes), the leader in producing Lithium-ion power systems that facilitate the transition from lead-acid batteries and Internal Combustion Engine (ICE) power to green Lithium-ion battery power, today announced its Swappable Mobile Power (SMP) portfolio. The SMP portfolio enables manufacturers to electrify their mobile and motive products utilizing swappable batteries with the leading Lithium-ion battery chemistry. At the center of the portfolio, the Swappable Industrial Battery (SWIB-1000) offers one of the highest Watt-Hour ratings for swappable Lithium Iron Phosphate (LFP) batteries on the market today.
Optimized for operator ergonomics and “hot” swapping of portable batteries, the SMP portfolio of products enables the electrification of non-powered mobile carts, such as industrial, medical or educational workstations. Additionally, multiple Swappable Industrial Batteries can be connected to power motive products with high torque requirements, such as Automated Mobile Robots (AMR), pallet jacks, or motorized sleds.
“Green Cubes pioneered the use of swappable batteries for mobile medical workstations and is the market leader in the production of swappable batteries for mobile industrial workstations,” said Mike Davis, Chief Revenue Officer for Green Cubes. “The Swappable Industrial Battery enables mobile workstation and motive product manufacturers to enhance the capabilities of their products and diversify their product line. This includes the electrification of non-powered workstations and motive products, as well as expanding the range of IT devices supported on existing powered workstations.”
The Swappable Industrial Battery is a 48 Volt, 20 Amp-Hour, 1000-Watt Lithium Iron Phosphate battery that offers exceptionally stable voltage under load, high capacity and power delivery in a small lightweight form factor. In addition to its ergonomic and ruggedized design, the watertight battery has an Ingress Protection (IP) rating of 65, which is optimized for both indoor and outdoor environments. Agency and safety approvals include UN 38.3 and IEC 62133.
To complement the Swappable Industrial Battery, the SMP portfolio has a suite of accessories to complete the integration with mobile workstations and motive products, including a battery receiver, power distribution electronics, AC/DC power supplies for charging and DC/AC power inverters to power mobile IT devices.
The SMP products are currently being evaluated by educational and industrial equipment manufacturers and their enterprise customers. Commercial availability is scheduled for the first quarter of 2023.
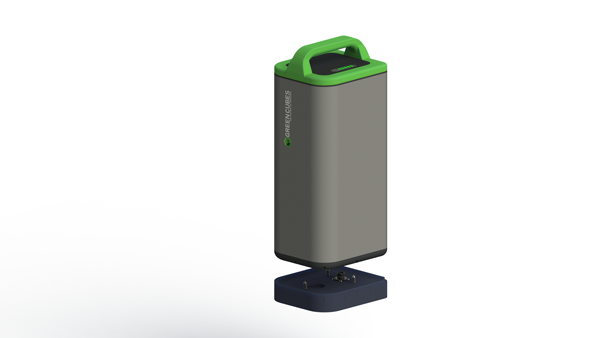
To learn more about the Swappable Mobile Power (SMP) portfolio; https://greencubes.com/product/industrial-battery-swib-1000/
About Green Cubes Technology
Green Cubes Technology develops and manufactures safe and reliable electrification solutions that enable its OEM and enterprise customers to transition from Lead Acid and Internal Combustion Engine (ICE) power to Lithium-ion battery power. Green Cubes utilizes proven hardware and software platforms to build the most reliable Lithium power solutions in its industries. With over 300 employees across six countries, Green Cubes has been producing innovative, high-performance, and high-quality power solutions since 1986.
Future-Proofing Your Fleet: Long term Viability of Li-ion Technology in the Material Handling Industry and Ground Support Equipment Industries
For nearly two decades, I have focused on battery technology and the battery industry. I have a PhD from The University of Texas at Austin, where I studied with John Goodenough, who won the Nobel Prize for inventing the Lithium-ion (Li-ion) battery. When I was in graduate school, in the late 90 and early 2000s, Li-ion batteries were not yet used commercially; laptop computers were powered by NiMH batteries and NiCd powered tools, camcorders and remote-control cars. GM had a robust research program on electric vehicles, which was ultimately canceled in 2002 because of poor market acceptance. No one knew which technology would power the emerging consumer electronics market- most thought NiMH batteries would stay as the default and big companies invested in everything from fuel cells to MEMs fly-wheels.
The Beginning of the Li-ion Battery Industry
Then, a number of key innovations resolved some of the safety concerns about Li-ion batteries, SONY commercialized the first Li-ion cells and the die was cast. Nearly all laptops were powered by Li-ion batteries within just a few years, and Li-ion batteries enabled cell phones which came on the market a bit later. The sheer volume of these two applications, enabled the market Li-ion battery market itself to mature, so that now nearly everything that needs portable or back-up power uses Li-ion. The only exception to this adoption is long term legacy lead acid stationary back up power and heavy equipment motive applications, like material handling and ground support equipment. Lead acid still has a lower up front cost and these applications don’t really benefit from the size and weight advantages of Li-ion batteries.
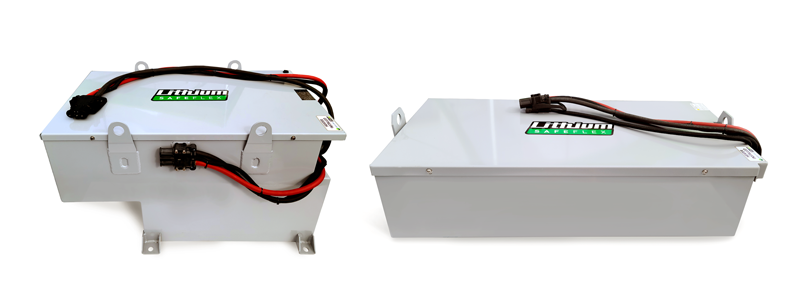
What will Happen Next in the Li-ion Battery Industry?
As motive applications like material handling and ground support equipment become the last hold outs for an older technology with a decidedly poorer environmental profile, I believe that we will see total costs for lead acid batteries increase. The infrastructure that is built up around the lead acid market (recycling, etc.) will shift to support the Li-ion battery industry. Li-ion batteries will have more suppliers and more diverse product offerings, more competition and more supply chain redundancy. Adjacent technology for Li-ion will improve and manufacturing methods will gain efficiencies. The US government is already beginning to invest heavily in strategic, domestic Li-ion manufacturing. When the governments of leading countries can start to ban and regulate Lead Acid, they will. In fact, RoHS and other regulations have specific call-outs for lead in batteries just because there has not been a viable alternative, until now. China has already begun to take drastic steps to completely ban lead acid battery manufacturing. Lead acid manufacturing will likely be only in far-away places with inexpensive labor and poor environmental regulations and high shipping and import costs. In the industry, there is no more debate about if Li-ion batteries will overtake Lead acid, the question is more when and how. The volume of Li-ion batteries being produced will be an advantage to the material handling and ground support industries long term, rather than a risk.
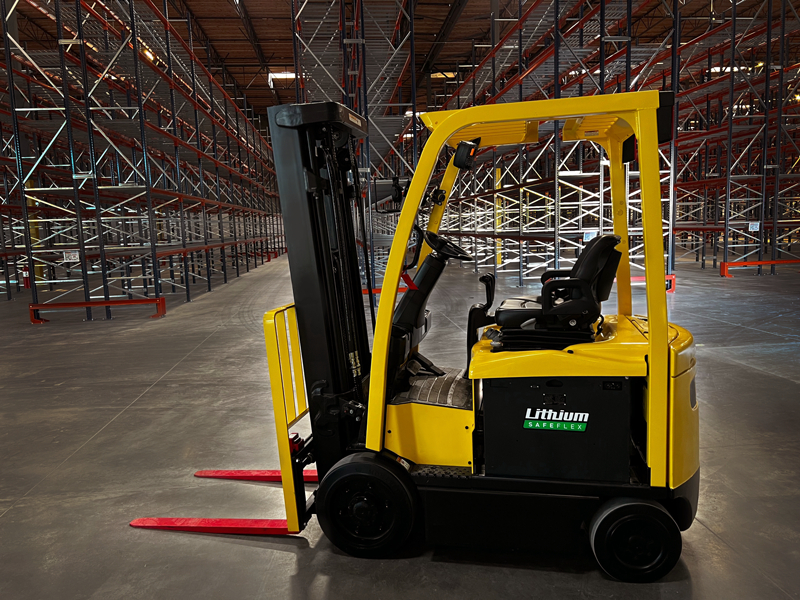
Will a New Technology Replace Li-ion Batteries?
The conversion of the entire industry from lead acid to Li-ion will be long, so you may wonder if there will be another, new technology that will leapfrog it, and my prediction is that there will not. Inventions in this science are very slow and tend to be incremental; it has taken China 25 years to get its mature Li-ion battery industry. If there were something coming up behind Li-ion batteries, it would already be far into development. I do believe that fuel cells will be a key part of the new zero carbon fleets, but they will replace ICE primarily and co-exist with Li-ion battery powered trucks. Because hydrogen infrastructure requirements are similar to gas and oil, it will likely be ten years before this technology is commonly available. In summary, Li-ion battery technology is going to be the de-facto standard in material handling and ground support equipment in the near future.