Why Choose Lithium SAFEFlex Batteries for Your Material Handling Operations?

30% Higher Charging Efficiency
Achieve 98% or higher charging efficiency, boosting productivity and reducing power consumption

Regenerative Power Capture
Capture up to 80% more regenerative energy for longer run times and less frequent recharging

Zero Maintenance Hassle
No dangerous gas emissions or watering requirements, thanks to the internal BMS module

Faster Charging
Recharge in just one hour without battery degradation, compared to 50% degradation in lead acid batteries
Upgrade to Lithium SAFEFlex Batteries Today!
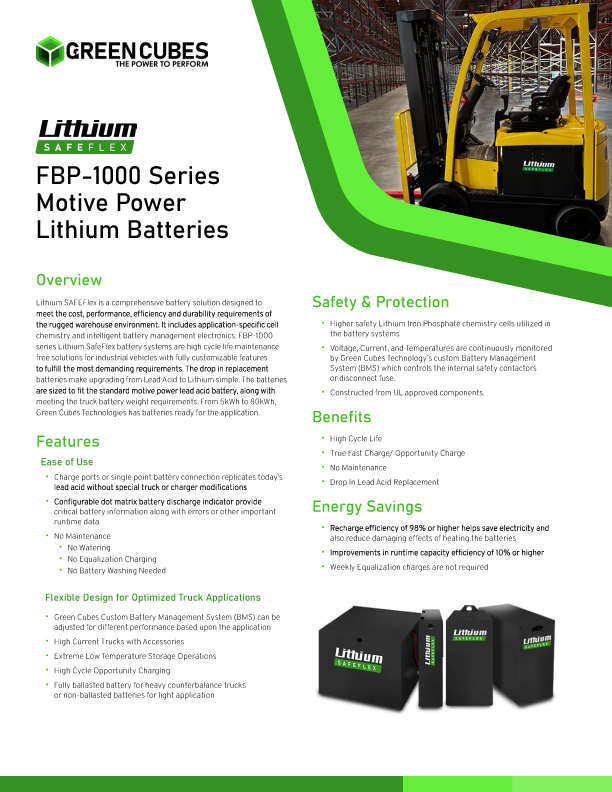