Overview
Workplace injuries are all-too common in the warehouses and battery maintenance for material handling equipment is a typical culprit. The ongoing maintenance required to keep flooded lead acid batteries running presents a danger to the workers tasked with charging, watering and changing batteries. Batteries power equipment on construction sites, in tractors, trucks and automobiles, and most of them contain hazardous substances like lead and sulfuric acid. Unless workers who maintain, recharge, and operate batteries know the risks and how to mitigate them, they can suffer severe workplace injuries. New Lithium-ion batteries eliminate most of these issues because they are self-contained and maintenance free. Iron phosphate, a subset of Li-ion is the safest chemistry available, and its long cycle life means that it will last the lifetime of the truck.
Learn about:
- Hazards and precautions for lead acid batteries
- The safety features of Li-ion batteries
- The advantages of iron-phosphate Li-ion batteries
Lead acid batteries: Hazards, Precautions and Maintenance
The charging of lead-acid batteries is hazardous, but many workers may not remember this since the activity is so routine.
The three most common risks are from hydrogen gas formed when the battery is being charged, the sulfuric acid in the battery fluid- with exposure from spills and leaks, and physical injuries from the batteries’ weight. Repetitive use injuries, such as sprains and strains are common, but unfortunately the highly corrosive electrolytes in batteries can cause respiratory irritation, eye damage, skin irritation, and it can even erode tooth enamel. The sheer size of material handling batteries means that crush injuries also occur during battery changes. The corrosive electrolyte material is shown in the first image below of a damaged lead acid battery.
This is an overview of the risky maintenance for lead-acid batteries:
- The fluid level is extremely important and a safe level requires regular watering. Overwatering and underwatering can both damage the battery. If too much water was added before charging, the electrolyte levels will expand and cause the battery to overflow and damage the battery.
- Conventional batteries contain a liquid “electrolyte” which is a mixture of sulfuric acid and water. The plates in a lead battery contain an active material that should be continuously bathed in electrolytes while oxygen and hydrogen gas are released during charging.
- When batteries are being recharged, they generate hydrogen gas that is explosive in certain concentrations in air, so the ventilation system must provide enough fresh air to prevent an explosion.
- The electrical voltage created by batteries can ignite flammable materials and cause severe burns. Workers have been injured and killed when loose or sparking battery connections ignited gasoline and solvent fumes during vehicle maintenance.
- Wear personal protection equipment such as protective eyewear and gloves when working on batteries. To avoid splashing acid, personal protective equipment such as chemical splash goggles and a face shield must be worn.
- First aid facilities, eye wash stations, and emergency showers are necessary to reduce the severity of accidental contacts.
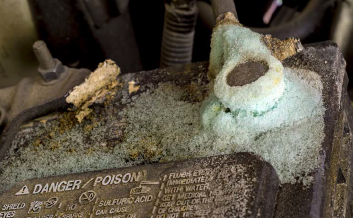
Safety Features of Li-ion batteries
Li-ion batteries are becoming more and more common because of their long cycle life and short charge times, but they also greatly reduce the risk to the workforce when they are implemented in a warehouse environment. Li-ion batteries are made up of cells, just like lead acid batteries. Large format Li-ion cells, used to manufacture batteries used for motive applications, are shown in the picture. The cells have an anode and a cathode with a separator and electrolyte in between. Unlike flooded lead acid cells, the li-ion cells are sealed and have many safety factors designed in them. The cathode material is the main determining factor in the cell’s performance. In the battery power market today there is a myriad of available battery cathode chemistries to choose from. It is a critical decision which not only impacts how well the product will operate but also how safely it can operate. Factors such as how much power is required, the time required to charge, operating temperatures, operating environment, packaging dimensions, and weight are all examples of key parameters that must be considered.
Li-ion batteries are becoming more and more common because of their long cycle life and short charge times, but they also greatly reduce the risk to the workforce when they are implemented in a warehouse environment.
While higher energy li-ion chemistries are available, Lithium iron phosphate (LFP) is safest with the longest cycle life due to its stable chemical make-up. A demonstration of how much more stable the LFP chemistry is compared to the high energy Lithium Cobalt Oxide (LCO), used in consumer electronics, is to compare the thermal runaway temperatures- the high temperatures at which the chemistries begin to become unstable and volatile. LCO has a much lower thermal runaway temperature of 150°C (302°F) compared to LFP’s thermal runaway temperature of 270°C (518°F). This large difference shows LFP to be the much safer of the two lithium chemistries.
High energy density is important for battery systems which need to be smaller and lightweight. A more modern cathode chemistry than LCO is Nickel Manganese Cobalt (NMC). NMC is the result of an attempt to balance safety and performance. A version of NMC is the chemistry is utilized in automotive EV battery systems today. EV batteries utilize higher voltages and with the higher energy available, additional safety measures and control must be implemented. The cells heat up quicker, so proper charging is critical.
With larger industrial, motive power battery systems, space is available for the larger batteries, and weight is actually needed for the counterbalance systems. Fast charging is critical and LFP accommodating lead acid charging helps with systems safety. Cycle life and safety is prioritized. The lower voltage of LFP is good match for Lead Acid replacement. This and the tolerance of Lead Acid charging systems make LFP the safest backward compatible option for material handling batteries.
The physical construction of the cell also affects its safety. All lithium batteries contain a critical component called the separator, which is placed in between the anode and cathode layers in the electrode. The separator limits the chemical reaction of the electrode and helps to prevent thermal runaways by closing its porous structure at high temperatures. The safest Li-ion cells incorporate ceramic separators. The ceramic material is resilient at high temperatures and helps prevent the breakdown of the separator that occurs during a thermal runaway event.
The electronics of the Li-ion battery also provide protection against safety events, with incorporated fuses and protection against over-charge, over-discharge and high and low temperature charging. These battery “smarts,” combined with the long cycle life and short charge time seamlessly integrate with the material handling equipment. The fact that the battery is virtually maintenance free over the life-time of the truck, eliminates the possibility for user error and greatly reduces the risks in the workplace.
With larger industrial, motive power battery systems, space is available for the larger batteries, and weight is actually needed for the counterbalance systems. Fast charging is critical and LFP accommodating lead acid charging helps with systems safety
LFP VS. NMC
Parameter | Lithium Iron Phosphate (LFP) | Nickel Manganese Cobalt (NMC) | Comparison |
---|---|---|---|
Voltage | 3.2 V | 3.7 V | NMC Batteries are lighter and more compact |
Weight Energy Density | 90-120 Wh/Kg | 150-250 Wh/Kg | |
Volume Energy Density | 300-350 Wh/L | 500-700 Wh/L | |
Max Discharge Rate | 30C | 2C | LFP Batteries provide more power over a shorter period, and can be charged faster |
Max Charge Rate | 10C | 0.5C | |
Typical Cycle Life (@80%) | 3000+ Cycles | 500-1000 Cycles | LFP Batteries will deliver more cycles over a longer calendar life |
Calendar Life (@80%) | 8-10 Years | **4-5 Years | |
Thermal Runaway Onset* | ~195 °C | ~170 °C | NMC Batteries have lower thermal runaway thresholds and will burn hotter |
Thermal Runaway Increase* | 210 °C | 500 °C | |
* Royal Society of Chemistry, 2014 ** With derated charge voltage |
YOUR NEXT STEP
Our engineers can help you identify areas of your operation where Lithium SAFEFlex can make the most impact, based on how you use your fleet:
- We’ll evaluate your facility to see where changing from Lead Acid to Li-ion will most impact your organization. Our analysis will cover number of vehicles, number of shifts, charging information, and major improvements you’d like to see.
- We’ll provide a quote to demonstrate that there will be a cost savings associated with the change to Li-ion and it’s safety benefits, then we’ll provide a trial system with monitoring software to validate the savings.
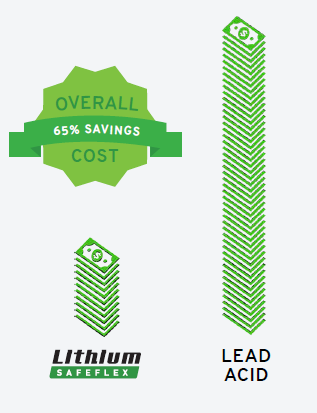
ABOUT GREEN CUBES TECHNOLOGY
Green Cubes Technology develops and manufactures a complete portfolio of lithium power systems that enable its OEM and enterprise customers to transition from Lead Acid and Internal Combustion Engine (ICE) power to Lithium-ion battery power. Green Cubes utilizes proven hardware and software platforms to build the most reliable lithium battery systems in its industries. With over 300 employees across six countries, Green Cubes has been producing innovative, high-performance, and high-quality products since 1986. For more information, email info@greencubestech.com or visit greencubestech.com.