Overview
In the battery power market today there is a myriad of available battery types to choose from. It’s a critical decision which not only impacts how well the product will operate but also how safely it can operate. Factors such as how much power is required, the time required to charge, operating temperatures, operating environment, packaging dimensions, and weight are all examples of key parameters that must be considered.
The Material Handling / Motive Power battery market requires some of the highest power products in the world so safety is a key parameter and necessity.
Safety by Design
The Green Cubes Technology engineering team has extensive experience in working with various battery technologies. This wealth of experience and knowledge of the various available battery technologies was used in selecting the optimal chemistry for the material handling market. By selecting Lithium Iron Phosphate (LFP) for the Lithium SafeFlex MH batteries the team utilized a lithium chemistry that is first and foremost known for its inherent safety.
Chemical structure
While higher energy lithium chemistries are available, LFP was selected due to its stable chemical make-up. The Phosphate & Oxygen bond is both thermally and chemically stable due to the single-dimensional lattice structure. Its 1 D lattice structure limits how lithium ions are transferred. This transference limitation enables improved stability and cycle life. A demonstration of how much more stable the LFP chemistry is compared to the longer established high energy Lithium Cobalt Oxide (LCO), i.e. the lithium battery used in consumer electronics, is to compare the thermal runaway temperatures, which are the high temperatures at which the chemistries begin to become unstable and volatile. LCO has a much lower thermal runaway temperature of 150°C (302°F) compared to LFP’s thermal runaway temperature of 270°C (518°F). This large difference shows LFP to be the much safer of the two lithium chemistries.
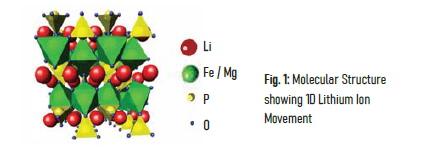
In addition to chemistry selection, the physical construction is an important parameter to consider in the design selection process. All lithium batteries contain a critical component called the separator, which is placed in between the anode and cathode layers in the electrode. The separator limits the chemical reaction of the electrode and helps to prevent thermal runaways by closing its porous structure at high temperatures. The Green Cubes team has selected cells which incorporate ceramic separators. The ceramic material is resilient at high temperatures and helps prevent the breakdown of the separator that occurs during a thermal runaway event.
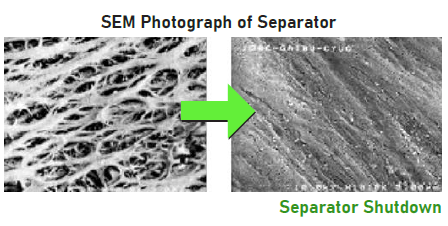
Safety by Product Experience
Over the past 20 years, Green Cubes Technology has designed and produced millions of lithium battery systems along with other chemistries such as NiMH, NiCd, and lead acid. Green Cubes has lifesaving batteries integrated in Lexus vehicles, mines, hospitals, and a multitude of other industrial and rough environment applications. Our Lithium SafeFlex batteries have specifically been utilized in onroad trucks in the US, electric vehicles across India, and in the material handling industry over the past 4 years. With over 30 years experience in Power, Green Cubes is an engineering driven company with its top focus on safety.
ABOUT GREEN CUBES TECHNOLOGY
Green Cubes Technology develops and manufactures a complete portfolio of lithium power systems that enable its OEM and enterprise customers to transition from Lead Acid and Internal Combustion Engine (ICE) power to Lithium-ion battery power. Green Cubes utilizes proven hardware and software platforms to build the most reliable lithium battery systems in its industries. With over 300 employees across six countries, Green Cubes has been producing innovative, high-performance and high-quality products since 1986. For more information, email info@greencubestech.com or visit greencubestech.com.